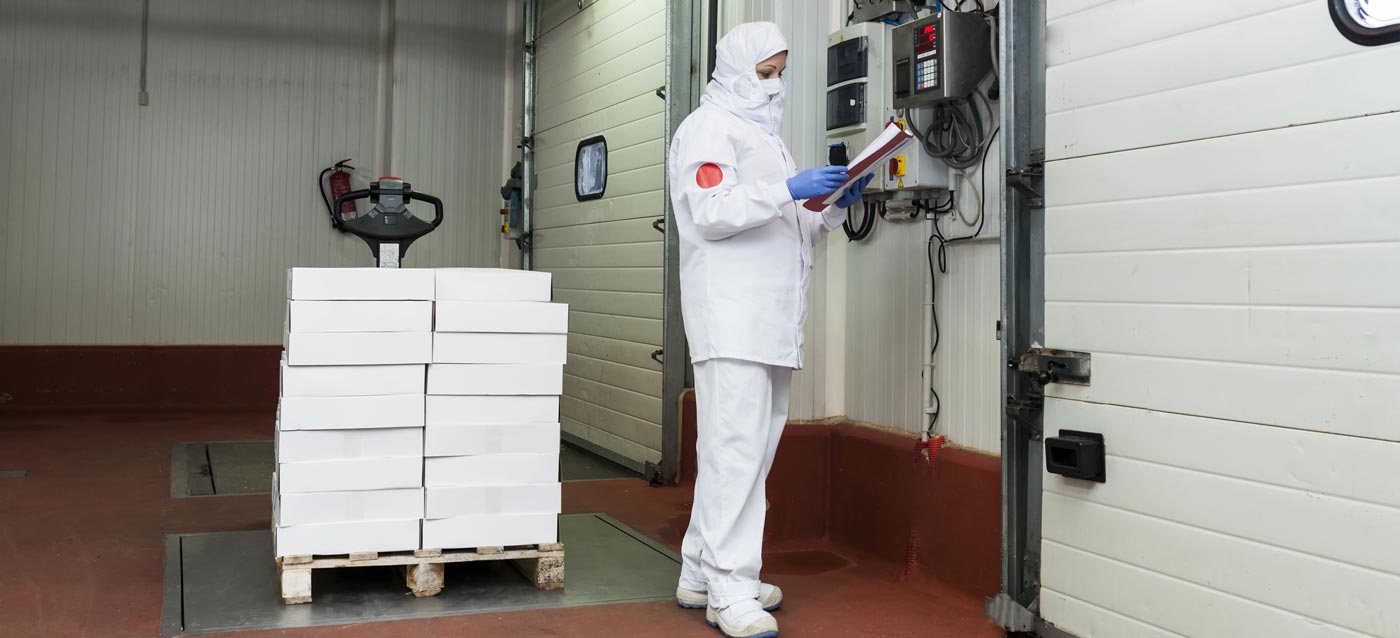
Thermal printer integration in weighing scales: challenges and solutions
Integrating thermal printers in weighing scale manufacturing presents both opportunities and challenges. Thermal printers offer fast, reliable, and high-quality printing for labels, receipts, and barcodes, making them an essential component in many industrial applications. However, mechanical engineers face several obstacles when integrating these printers into scales, including compatibility with existing systems, space constraints, power requirements, and media management.
A seamless integration requires careful planning, the right hardware selection, and a thorough understanding of how thermal printers interact with the weighing scale’s mechanics and software. This article explores the most common challenges engineers encounter and provides practical solutions to ensure smooth and efficient integration.
Compatibility with existing systems
Challenge
One of the biggest challenges in integrating thermal printers into weighing scales is ensuring seamless compatibility with existing systems. The printer must communicate effectively with the scale’s control system, whether it’s a programmable logic controller (PLC), distributed control system (DCS), or custom software. Any misalignment can lead to delayed or inaccurate printouts, disrupting workflows and causing data inconsistencies.
Beyond system compatibility, engineers must also address integration with data management systems. Many scales are linked to inventory tracking, quality control, or regulatory compliance software. A poorly integrated printer can lead to missing transaction data, misprinted labels, or delays in updating critical records, affecting efficiency and compliance.
Solutions
To ensure seamless integration, engineers should:
- choose printers with multiple connectivity options, such as RS232 or USB to match system requirements.
- verify firmware compatibility with the scale’s software and ensure it supports industry-standard communication protocols.
- implement APIs and custom drivers for smooth data exchange between the printer and the scale’s control system.
- conduct pre-integration testing to identify software conflicts and resolve them before full deployment..
By addressing both hardware and software integration, manufacturers can ensure that the thermal printer functions as an integral part of the weighing scale, eliminating print errors, enhancing traceability, and improving overall efficiency.
Space constraints and mounting issues
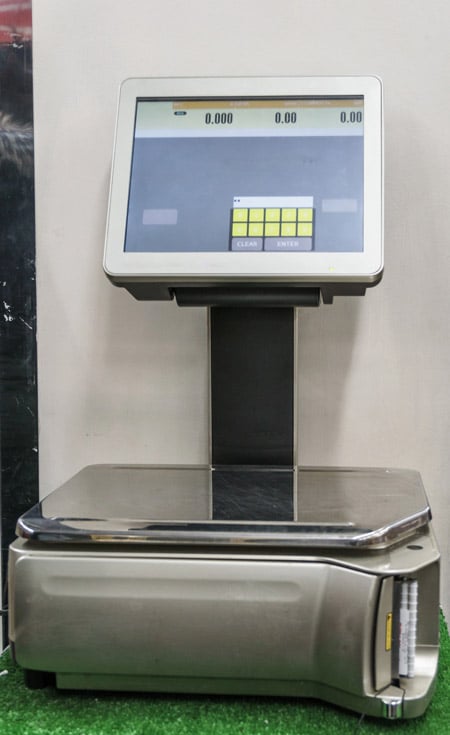
Challenge
Many weighing scales, particularly those used in compact or mobile applications, have limited space for additional components.
Engineers must find ways to integrate the thermal printer without interfering with other critical parts of the scale. Poor placement can lead to difficulties in accessing the printer for maintenance or paper replacement, ultimately disrupting workflow.
Solutions
To overcome space limitations, engineers should:
- select compact thermal printers specifically designed for integration into small spaces.
- evaluate mounting flexibility by considering vertical, horizontal, or custom enclosure options that align with the scale’s design.
- use ergonomic placement to ensure easy access for paper loading and maintenance.
- explore modular integration options, allowing the printer to be attached externally while still functioning seamlessly with the scale.
With careful planning, even the smallest weighing scales can accommodate a thermal printer without compromising usability or functionality.
Power requirements and energy efficiency
Challenge
Thermal printers have specific power requirements, and improper integration can lead to inefficiencies, increased energy consumption, or system instability. In some cases, a scale’s existing power supply may not support the printer’s voltage and current needs, resulting in inconsistent performance or hardware damage.
Solutions
To ensure a stable and energy-efficient integration, engineers should:
- select low-power consumption models that align with the scale’s power capacity.
- verify voltage and current compatibility between the printer and the power source.
- opt for thermal printers with power-saving features, such as sleep mode, to reduce energy consumption during idle periods.
- distribute power load effectively to prevent voltage drops or fluctuations that could affect printing performance.
By addressing power requirements early in the design process, engineers can prevent operational disruptions and improve the overall efficiency of the weighing scale system.
Media management and print quality
Challenge
Selecting the right printing media is essential for producing high-quality labels, receipts, and barcodes in weighing scale applications. Engineers must ensure that the printer supports the correct paper width, thickness, and roll size while also considering the specific application—whether it’s ticket printing or linerless labeling.
- Ticket printing requires durable thermal paper that can withstand handling, environmental exposure, and long-term readability.
- Linerless labeling is gaining popularity in weighing scales for logistics, food retail, and industrial applications. Unlike traditional labels, linerless labels reduce waste, improve sustainability, and offer greater flexibility in label length. However, they require specialized thermal printers designed to handle adhesive-free media without jamming.
Additionally, maintaining high print quality is crucial for barcode scanning, regulatory compliance, and brand consistency. Poor print quality can lead to misread labels, operational inefficiencies, and increased costs.
Solutions
To optimize media management and print quality, engineers should:
- choose a printer with adjustable print settings to accommodate different paper types, including ticket paper and linerless labels.
- select high-resolution (DPI) printers to ensure sharp, scannable barcodes and clear text.
- opt for easy-loading mechanisms to simplify roll replacement and minimize downtime.
- ensure compatibility with linerless labels by selecting printers with non-stick coatings and specialized paper-feeding systems to prevent adhesive buildup.
- test paper durability and print longevity to ensure that receipts and labels remain readable over time.
By prioritizing media compatibility and print accuracy, manufacturers can enhance the reliability, efficiency, and sustainability of their weighing scales while reducing waste and maintenance issues.
Durability in harsh environments
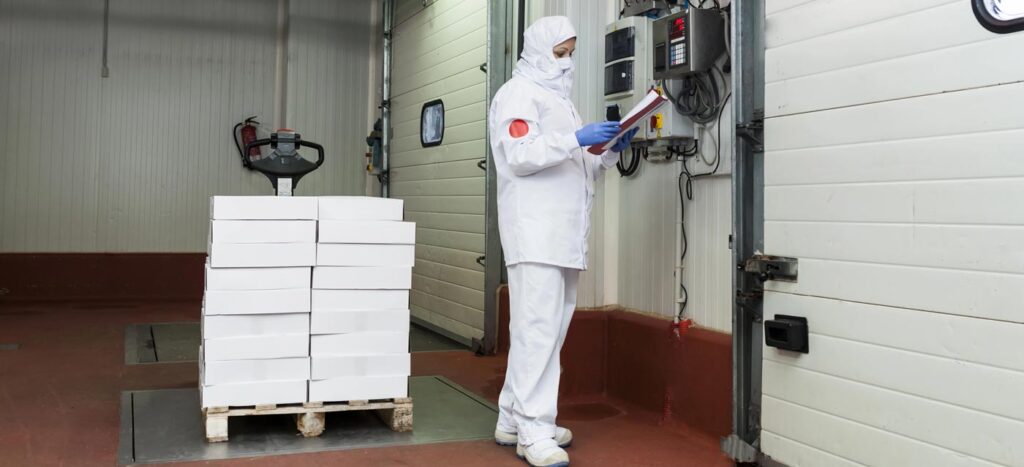
Challenge
Weighing scales are often used in demanding environments such as industrial warehouses, food processing plants, and outdoor locations. These settings expose thermal printers to dust, moisture, temperature fluctuations, and mechanical vibrations. If not properly designed for such conditions, the printer’s performance and lifespan can be significantly reduced, leading to frequent breakdowns and costly maintenance.
Solutions
To ensure long-term durability and reliability, engineers should:
- choose rugged thermal printers with sealed enclosures that protect internal components from dust and moisture.
- use vibration-resistant mounts to minimize mechanical stress in high-movement environments.
- select printers with wide operating temperature ranges to withstand extreme hot or cold conditions.
- consider models with corrosion-resistant materials, particularly for food and chemical industries where exposure to liquids is common.
By selecting a durable and industrial-grade thermal printer, manufacturers can minimize operational disruptions and extend the lifespan of their equipment.
Compliance with industry regulations
Challenge
Weighing scales used in commercial, industrial, and medical applications must comply with various regulatory standards. Thermal printers integrated into these scales must meet safety, environmental, and quality control requirements to ensure compliance with industry guidelines. Failure to adhere to these regulations can lead to legal issues, rejected products, or additional certification costs.
- Common concerns include:
- adherence to environmental guidelines, such as the EU RoHS Directive, which restricts hazardous materials in electronic devices.
- compliance with safety and emissions standards (e.g., CE, UL, FCC).
- barcode readability for regulatory or inventory tracking purposes.
Solutions
To ensure compliance, engineers should:
- select thermal printers certified for industrial or medical use, depending on the application.
- verify barcode and label accuracy, ensuring that printed information meets industry standards for traceability and scanning.
- choose RoHS-compliant printers that minimize environmental impact by avoiding restricted substances.
- stay updated on changing industry regulations, ensuring that the printer integration remains compliant with evolving requirements.
By prioritizing compliance, manufacturers can avoid costly regulatory setbacks and ensure their weighing scales meet all necessary industry standards.
Maintenance and long-term reliability
Challenge
Thermal printers in weighing scales are often subjected to continuous operation, making reliability and ease of maintenance critical factors. Frequent paper jams, printhead degradation, or mechanical failures can lead to downtime and increased maintenance costs. If maintenance is complex, technicians may require extensive training, further delaying repairs.
Common issues include:
- difficulty in accessing printer components for repairs or replacements.
- printhead wear leading to poor print quality.
- dust and debris accumulation, causing paper feed issues.
Solutions
To ensure long-term reliability, engineers should:
- select printers with long-life printheads designed for high-duty cycles.
- opt for easy-maintenance designs, such as tool-free printhead replacement and quick-access compartments for loading paper rolls.
By selecting durable and easy-to-maintain thermal printers, manufacturers can reduce operating costs and extend the lifespan of their weighing scale systems.
Why APS is the ideal partner for weighing scale thermal printing solutions
Integrating thermal printers into weighing scales requires careful consideration of system compatibility, space constraints, power efficiency, media management, durability, regulatory compliance, and long-term reliability. Each challenge, if not addressed properly, can lead to inefficiencies, increased costs, and system failures. However, with the right approach and the right printing solutions, manufacturers can ensure seamless integration that enhances accuracy, productivity, and compliance.
At APS, we understand the complexities of thermal printer integration in weighing scale manufacturing. With over 20 years of expertise in thermal printing technology, we design and manufacture high-performance printers that offer compact footprints, robust durability, energy efficiency, and seamless system compatibility. Our printers are built to withstand harsh industrial conditions, ensuring consistent high-quality printing in even the most demanding environments.
As an industry leader, APS offers tailored solutions to meet the unique needs of weighing scale manufacturers. From custom mounting options to advanced connectivity and API integration, our engineering teams work closely with manufacturers to ensure flawless integration. Our ISO-certified production facilities and compliance with global standards guarantee that APS printers deliver long-term reliability with minimal maintenance, reducing downtime and total cost of ownership.
Whether you need a compact printer for a space-constrained scale or a rugged solution for industrial environments, APS provides cutting-edge technology that ensures seamless performance, precision, and durability.
Want to learn more? Download our whitepaper to get an in-depth guide on overcoming integration challenges and selecting the best APS thermal printer for your weighing scale application.
Take your weighing scale printing to the Next Level !
Looking for the perfect thermal printer for your weighing scale application? Contact APS today and let our experts help you find the ideal solution tailored to your specific needs.